How to design a product for deep drawing
Drawing is a popular method for manufacturing complex hollow products with an opening on 1 side. Most fabricators have learned to design a part for techniques such as turning and milling, however, designing a deep-drawn part requires a different way of thinking. Deep-drawing is one of many sheet metal fabrication techniques available, including bending, cutting, hydroforming, forging, thin-drawing, punching, flanging, beading and stretching
.
Differences between deep drawing and machining
In essence, the biggest difference between machining and deep drawing is the fact that machining removes material and deep drawing deforms material. Understanding these two key differences is the core to successfully designing a deep-drawn part. Below is a cross-section of the starting material for machining and deep drawing and the corresponding end result.
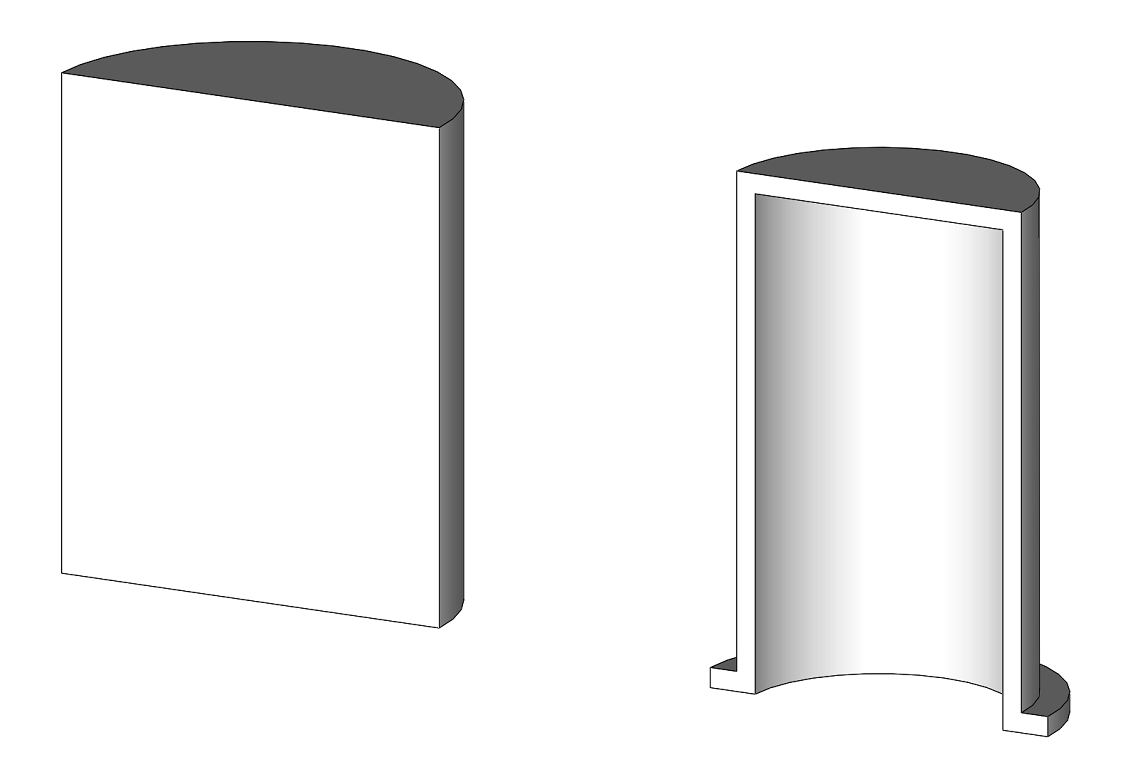
In machining, the intention is to remove the material effieciently and precisely. The material that remains is the requested product.
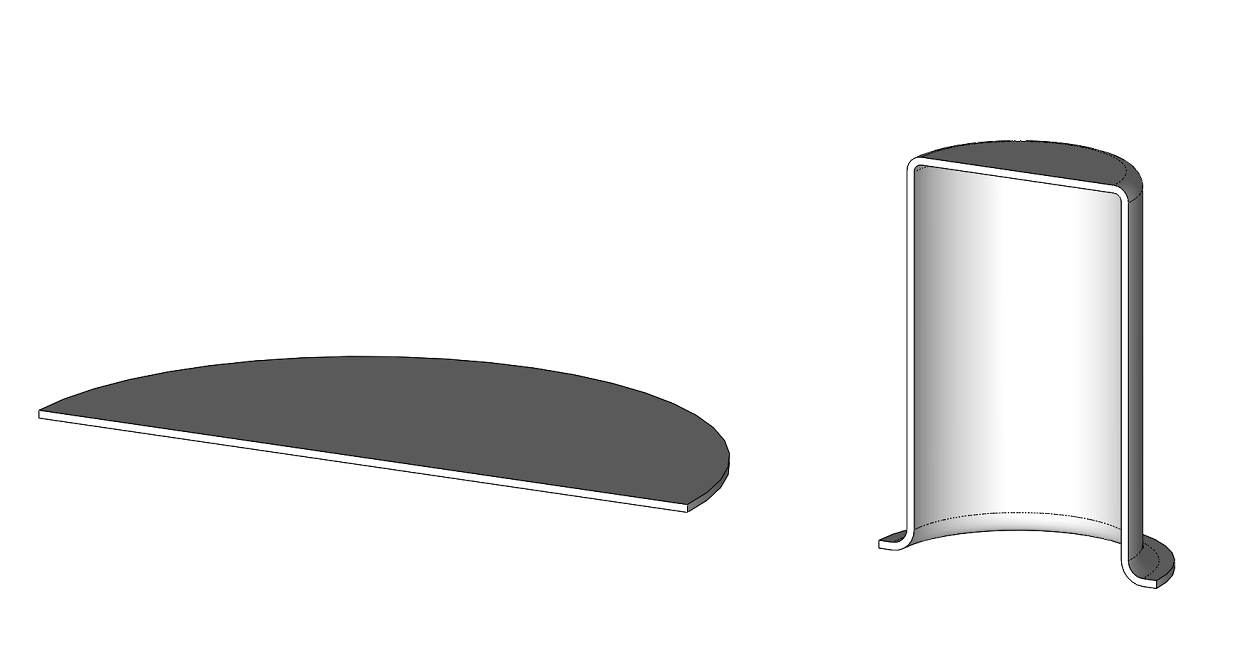
In deep drawing, a flat sheet (platine) is started and is deformed into a hollow 3d shape. The sheet is cold deformed which means that molecular structures are shifted relative to each other in the material.
Major differences between deep drawing and machining
Because of the differences between these techniques, it is important to think about the advantages and disadvantages that both technologies have to offer. See an article here that includes more information about the different techniques. Below is a brief summary of the main differences
.
Deep drawing | Machining | |
---|---|---|
Different wall thicknesses | In essence, the wall thickness is equal to the thickness of the sheet material with which it was started, however, the material can be thinned to a certain extent during the process | No limitations in making different wall thicknesses |
Thin walls | Very thin walls up to 20 microns possible. | Wall thicknesses below 0.2mm become challenging when turning. This is caused by the mechanical forces carried out on the product during machining. |
Strength and weight | Deep drawing gives high strength as the material hardens during the process. In general, products are lighter and stronger compared to machined products. | The strength of the material does not change during the process. However, through heat treatment it is possible to give some materials a higher hardness, but this may adversely affect dimensional accuracy. Products are generally heavier than deep drawn products. |
Aantallen | Very scalable. Often used at high volumes, but it can be interesting from as little as 100 pieces | Suitable for smaller series and prototypes |
Basic rules when designing a deep draw product
.
1) Flared products
Products that extend outward are generally not possible to make. Thus, the product cannot be larger than the dimensions of the draw mandrel. The draw mandrel cannot push the material outward. Besides the fact that the punch cannot push the material outward, it is also not possible to release the product from the draw ring in this way. However, there are other possible techniques to be able to make these products, such as with hydroforming. Please contact us if you have any questions regarding these types of parts.
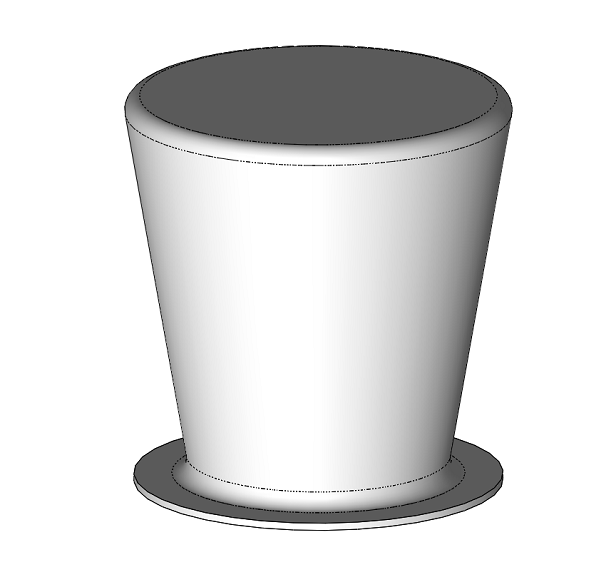
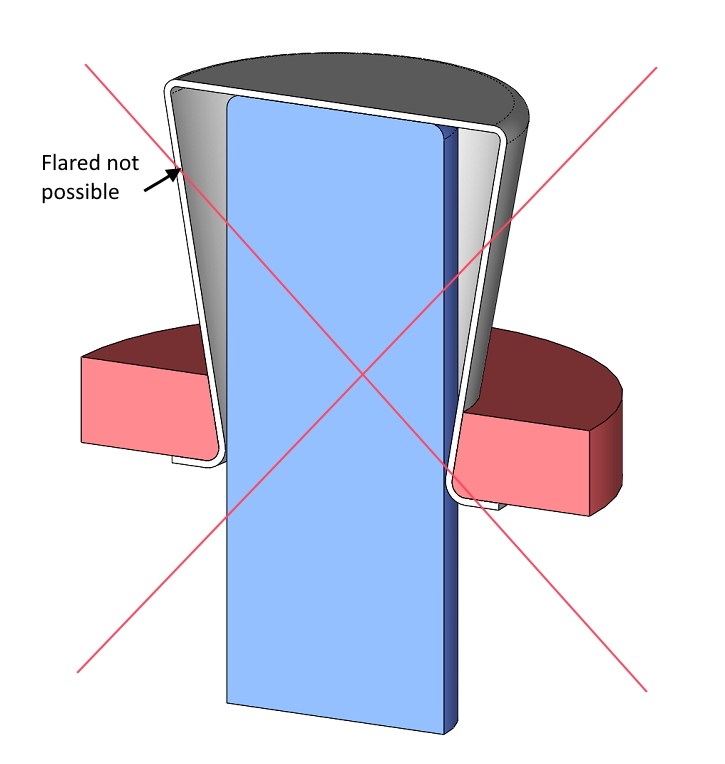
2) Products with walls thicker than the initial material
Products with walls thicker than the initial material (plating) are not possible to make using deep drawing, see left. Sometimes there are possibilities to draw the material thin. This involves starting with a product with a thick wall thickness and thinning the wall lengthwise. In this process the bottom retains its thickness and the wall becomes thinner and higher. Ask us about the possibilities
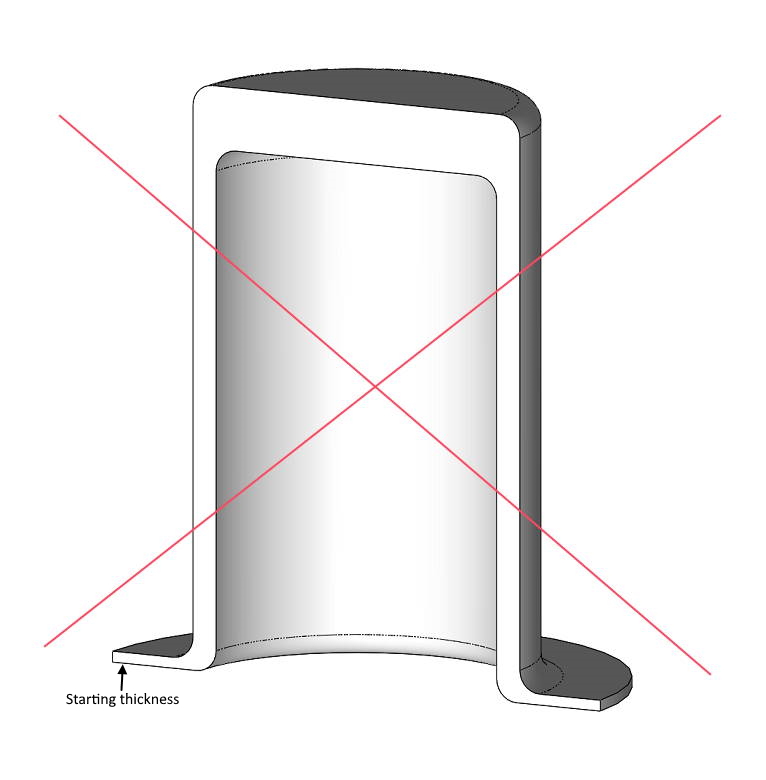
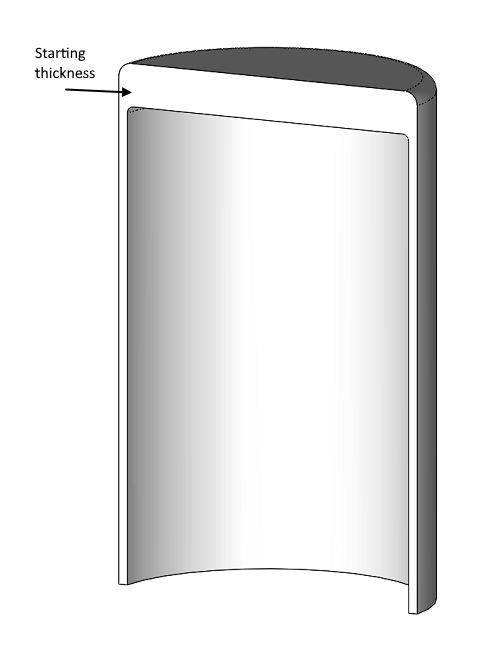
3) Cutting the flange
.
Vertical cutting is and basic simpler because this cutting motion is in line with the motion of the press. Cutting perpendicular to the wall is possible, but will require more complex tooling with the potential for higher wear. In addition, it is also possible to perform the cutting using secondary techniques outside the deep drawing process. These include laser cutting. Perpendicular cutting is therefore more costly.
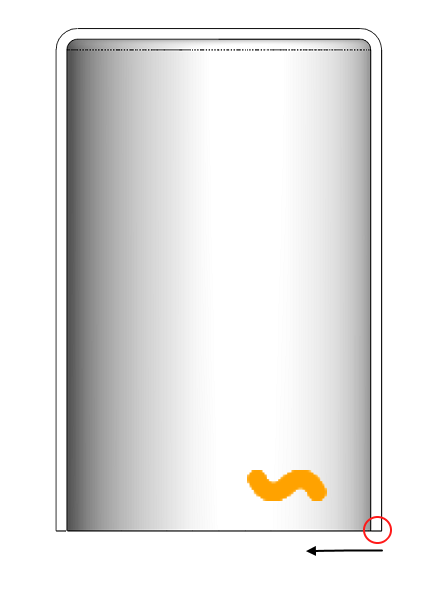
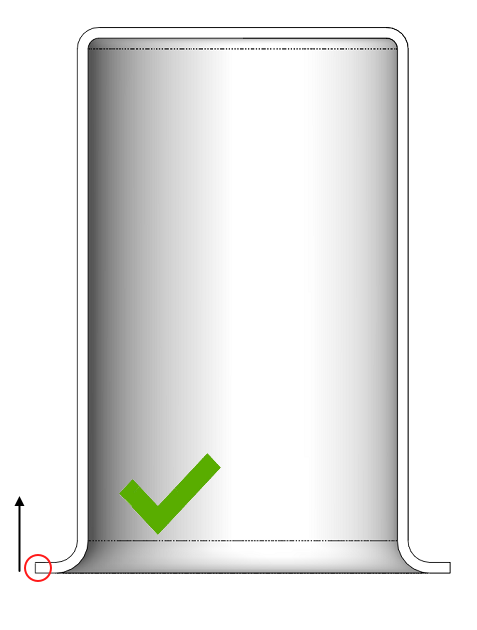
4) Ratio between diameter and material thickness
.
Products with a small diameter wall thickness ratio cannot be pulled deeply. The draw mandrel transfers the force of the press to the bottom of the product. The example below shows that the walls are so thick that the bottom has to handle too much force to deform the walls. Therefore, if a small diameter is desired, it is necessary to also adjust the thickness of the material accordingly.
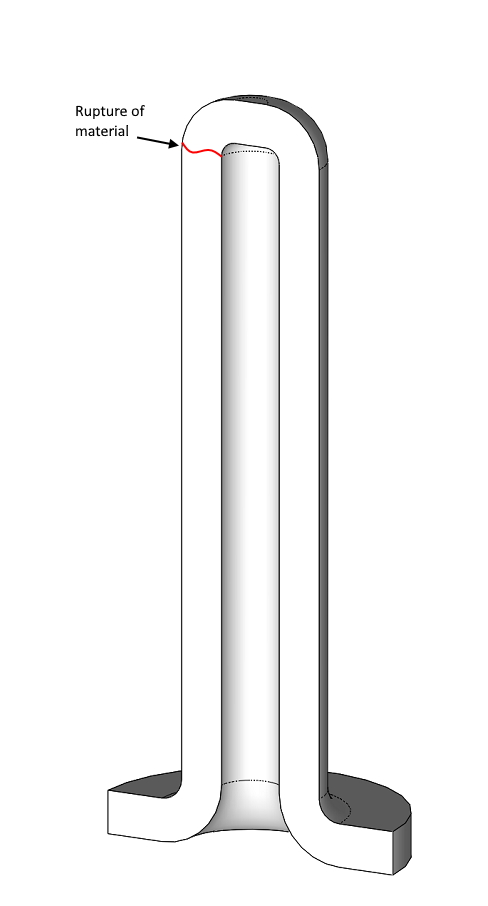
These are just a few examples to consider when designing a deep-drawn product. Look here for more information on deep drawing or go to the main page for more information. To find out if deep drawing is right for your application, contact us or email info@mubion.com