Advantages of deep drawing over machining
Deep drawing is one of the most popular methods of metal sheet processing. In hot stamping, flat sheet is transformed into a three-dimensional product using a punch and draw ring. See this article for a further explanation of the deep-drawing process and its differences from stretching material.
7 reasons to choose deep drawing
Micro deep drawing has many applications such as disposables for in medical applications or housings for sensors. It is widely used for parts in the automotive, electronics, optical, medical and aural industries, among others. This is due to the following advantages the process has.
1. Scalable.
Deep drawing is easily scalable and ideally suited for large volumes
2. Cost-effective.
After initial tooling costs, production costs are low.
3. Stable.
The manufacturing process is very stable, with little fluctuation in size.
4. Little waste.
Little waste is created in deep drawing
5. Seamless.
Because deep-drawing products consist of one part, there are no seams, transitions and weakening.
6. High strength.
During the process, the material naturally strengthens itself, eventually achieving high strength.
7. Wall thicknesses.
Very small wall thicknesses are possible. This can give advantages with, for example, temperature sensors that must be able to react quickly to temperature changes.
In general, there are some fundamental differences between deep drawing and machining.c
Deep drawing
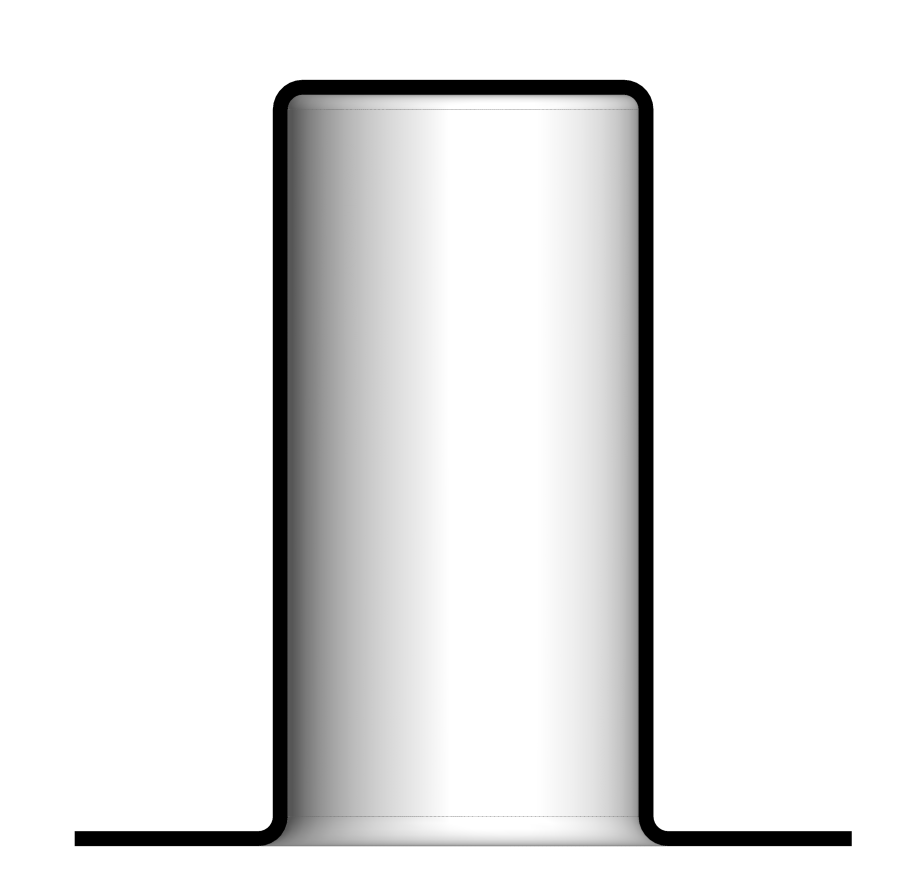
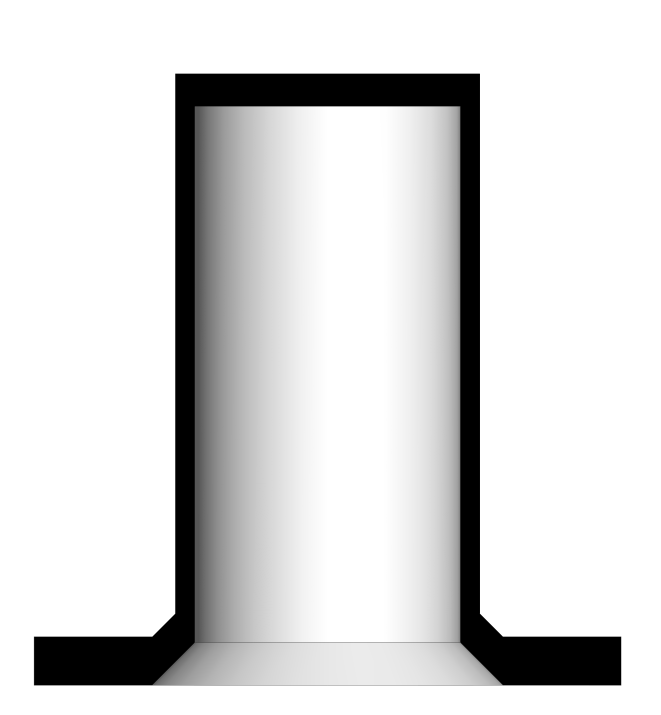
Machining
Deep drawing of medical components and disposables
Turning is an operation that is widely used in metal processing; as a result, there are many suppliers offering this technique. Turning is widely used in mechanical engineering when manufacturing prototypes, single pieces or small series. Below are the main reasons for choosing micro deep drawing instead of turning.
1. Scalability and cost.
This is also often the most important advantage. For (serial) quantities starting from +/-50 pieces, deep drawing can already be competitive.
2. For very thin walled products.
With deep drawing it is possible to deform material thicknesses up to 20 microns. Turning does not offer this possibility.
3. Product weight.
Because of the minimum thickness, strong yet lightweight products can be made. This is often unmatchable with turning.
4. With asymmetrical shapes.
Deep drawing gives an extreme freedom of shape: round, square, oval shapes can be made without any problems. By turning, only round shapes can be made.
5. Additional operations.
Additional operations such as holes or recesses can be integrated into the process, whereas turning requires this to be done on other machines.
6. High strength.
The fact that a thermoformed product is taken from rolled sheet means that the molecules have already been pressed flat. This structure of flat molecules means that sheet is naturally more rigid than cast material. In addition, the deformation during deep drawing provides
Micro deep drawing vs milling
In addition to turning, milling is also a machining technique that is widely used. Compared to turning, there are some differences.
1. Scalability and costs.
Milling is a time-consuming process on often expensive machines and is even less suitable for serial production than turning.
2. Complexity.
Milling has more freedom of shape than deep-drawing and also allows for different wall thicknesses.
Conclusion
If a suitable production technique must be found for a product, the first thing to consider at the outset is the expected numbers. If these are towards serial production, then deep drawing is quickly an obvious production technique. The list below presents the main arguments for choosing deep drawing.
Wondering what micro deep drawing can do for your issue? If so, please contact us.